Máy uốn phanh ép chủ yếu thực hiện việc uốn tấm theo phương thẳng. Bằng cách sử dụng các khuôn và thiết bị xử lý đơn giản, tấm kim loại có thể được ép thành một hình dạng hình học nhất định, và nó cũng có thể được xử lý bằng cách kéo căng, đột dập, đột dập và ép gấp nếp. Trong thực tế sản xuất, máy dập CNC chủ yếu được sử dụng để uốn các hình dạng hình học khác nhau của hộp kim loại, vỏ hộp, dầm hình chữ U và hình chữ nhật. Quá trình gia công của nó có ưu điểm là độ thẳng uốn cao, không có vết răng, không bong tróc, không có nếp nhăn, v.v.
Với sự phát triển không ngừng của công nghệ sản xuất máy uốn CNC, những ưu điểm của nó như độ chính xác định vị cao, tiện lợi, bù nhiễu hoạt động bằng 0 và tính nhất quán tốt của các sản phẩm gia công ngày càng được đa số các công ty sản xuất kim loại tấm ưa chuộng. Tuy nhiên, với những mong muốn có hạn, việc làm thế nào để sử dụng máy uốn tốt hơn, phát huy hết công năng và ưu điểm của nó đã trở thành một vấn đề mà các nhà sản xuất sử dụng máy uốn phanh CNC quan tâm và cấp thiết giải quyết. Trong quá trình sản xuất và sử dụng lâu dài, Zhongrui đã mở rộng hiệu quả các chức năng của máy uốn và tích lũy kinh nghiệm thông qua việc bổ sung các công cụ phụ trợ, chuyển đổi khuôn mẫu hiện có và sử dụng linh hoạt địa điểm. Bài viết này lấy máy dập CNC DA66T của Zhongrui làm ví dụ và giới thiệu chi tiết các kỹ năng sử dụng.
Thêm dụng cụ phụ trợ
Nếu bạn muốn làm cho máy công cụ phanh ép linh hoạt và dễ sử dụng, việc bổ sung thêm các dụng cụ phụ trợ là điều cần thiết. Việc gia tăng công cụ phụ trợ không chỉ có thể mở rộng phạm vi gia công của máy công cụ uốn CNC mà còn nâng cao hiệu quả xử lý.
1) Tấm chuyển tiếp (tấm giữa được hỗ trợ cho khuôn nhanh)
Chiều cao mở của máy uốn là khoảng cách giữa bàn làm việc trên và dưới. Vì máy uốn CNC DA66T có chiều cao mở lớn hơn, hãy cân nhắc sử dụng lỗ mở lớn để mở rộng phạm vi gia công. Như trong Hình 1, việc thêm một tấm chuyển tiếp khác vào tấm chuyển tiếp ban đầu có thể tăng chiều cao uốn bên của chi tiết (lên đến 85 mm), do đó có thể thực hiện gia công sâu với các mép uốn bên cao hơn. Bảng chuyển tiếp tự chế tạo có thể tùy chỉnh độ rộng của bảng chuyển tiếp theo các bộ phận thông thường của riêng bạn và nó phù hợp nhất để gia công các bộ phận có chiều rộng nhỏ với các cạnh uốn cao hơn ở cả hai bên.
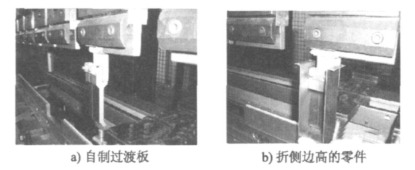
2) Góc của bảng điều khiển phía trước
Như hình 2, mặt trước của máy được trang bị một góc, có thể đặt các bộ phận nhỏ và giảm thời gian lấy các bộ phận. Đồng thời, một bàn làm việc nhỏ được lắp đặt để thuận tiện cho việc xử lý và thu thập các phôi nhỏ.
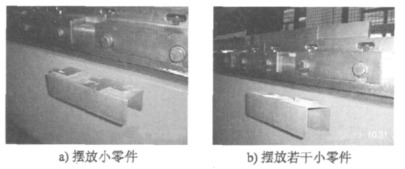
Tận dụng hết khuôn
Việc sử dụng máy uốn phanh dập CNC chủ yếu dựa vào khuôn trên và khuôn dưới. Nếu số lượng khuôn ít và ứng dụng không linh hoạt, phạm vi gia công của máy công cụ sẽ bị hạn chế rất nhiều. Vì vậy, trong những điều kiện cố định, làm thế nào để phát huy tối đa chức năng của khuôn hiện có thông qua tổ hợp tối ưu và biến đổi từng phần là một vấn đề mà người sử dụng máy công cụ nào cũng phải suy nghĩ. Sau đây là chức năng mở rộng mà chúng tôi sử dụng trong việc sử dụng bằng cách thay đổi khuôn của máy uốn CNC. Giới thiệu.
1) Mũi mài khuôn trên R
Khi khuôn trên được sử dụng trong một thời gian dài, độ mòn của khuôn trên của nó sẽ thay đổi bất thường. Chiều cao của khuôn thay đổi và độ chính xác uốn không thể được đảm bảo. Bằng cách mài, sửa đầu R và khớp với rãnh hình chữ V lớn hơn, các tấm dày có thể được gấp lại. Điều này kéo dài tuổi thọ của khuôn.
2) Thay đổi khuôn mẫu phế liệu để đạt được mức độ
Trong trường hợp không có khuôn uốn tổng hợp, việc giải quyết vấn đề hình thành cách ép mép chết là một ví dụ. Cạnh chết là một hình dạng uốn cong trong đó hai lớp chồng lên nhau, và thường được sử dụng để gia cố. Nhìn chung, bo mạch trên 2 mm hầu như không có cạnh chết. Ép mép chết cần được tạo hình bằng khuôn uốn hợp chất và nó phải được chia thành nhiều hơn hai quá trình để được hình thành.
Phương pháp thường được sử dụng là sử dụng khuôn uốn phức hợp, như thể hiện trong Hình 3. Trong bước đầu tiên, vật liệu được gấp đến 30 °, và trong bước thứ hai, góc uốn 30 ° được đặt ở đầu trước của khuôn phức hợp, và vật liệu được gấp lại thành một cạnh chết. Nhưng chúng tôi không có khuôn uốn tổng hợp, chỉ có khuôn uốn góc 30 °. Hoàn thành bước đầu tiên của khuôn uốn composite với khuôn có sẵn, bước thứ hai chỉ có thể tìm phương pháp khác. Bước thứ hai, khuôn trên và khuôn dưới đều phẳng. Sau khi phân tích, phần giữa của khuôn dưới rãnh chữ v kép hiện có có thể được sử dụng làm phần mặt phẳng và khuôn trên đang tìm kiếm mặt phẳng. Lấy khuôn trên đã loại bỏ hiện có ra và mài mép dao thành kiểu phẳng, như vậy sẽ giải quyết được vấn đề hình thành của vết dập mép chết.
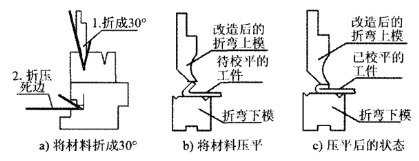
Sử dụng bộ khuôn sửa đổi này cũng có thể được làm phẳng. Trong thực tế gia công, người vận hành máy công cụ đôi khi mắc sai lầm, bao gồm uốn mép hoặc uốn kích thước không bằng nhau. Trong trường hợp yêu cầu bề mặt của chi tiết không cao, việc cạo bỏ chi tiết đó là điều đáng tiếc, chỉ nên gõ phẳng mép uốn. Knockout rất tốn công sức, nhưng có thể dễ dàng san bằng cách sử dụng tổ hợp khuôn trên. Các bộ phận có thể dễ dàng ép bằng tay vào khuôn trên và khuôn dưới, sau đó các bộ phận được làm phẳng bằng máy uốn CNC.
Kỹ năng trong quá trình hoạt động
1) Vị trí của khuôn uốn và vật liệu gia công
Khi sắp xếp kế hoạch, các yếu tố sau đây cần được xem xét:
Một. Sắp xếp các vật liệu có cùng độ dày với nhau;
b. Sắp xếp các khuôn của cùng một mô hình với nhau;
C. Các khuôn có hình dạng tương tự được sắp xếp với nhau.
Điều này có thể làm giảm thời gian và tần suất thay thế khuôn.
2) Định vị góc phải của các bộ phận hẹp và nhỏ
Khi phần uốn hẹp và dài, không dễ định vị. Trong quá trình gia công thường xảy ra hiện tượng định vị sau quyết định, chi tiết uốn cong dễ bị nghiêng. Do đó, sử dụng phương pháp được sử dụng trong Hình 4, khuôn được dán vào khuôn dưới để đảm bảo góc vuông. Khi uốn thế này, chi tiết không dễ bị nghiêng.

3) Uốn các bộ phận hình tam giác
Khi các chi tiết uốn cong, các chi tiết có góc cạnh sắc nhọn không dễ gần với quy luật phía sau. Nói chung, khi kích thước nhỏ nhất L ≤10 mm ngay sau quy tắc, thiết bị định vị cần được xem xét. Trong công việc thực tế, thiết kế và quy trình rất dễ bị bỏ qua, và những vấn đề như vậy thường xảy ra. Khi gia công, theo kích thước của chi tiết, người ta xác định một mảnh đơn được căn chỉnh với khuôn uốn và mảnh kép được căn chỉnh với lớp nền.
4) Thêm bản mỏng R
Do nhu cầu khác nhau của khách hàng nên giá trị R yêu cầu trên mép uốn cũng khác nhau. Trong quá trình gia công, đối với những chi tiết không yêu cầu độ chính xác về kích thước cao thì sử dụng tấm nền để tăng giá trị R để sau khi uốn đạt được giá trị R yêu cầu. Theo yêu cầu thiết kế, R dùng để chỉ quan hệ giữa V và R trong để chọn chiều dày tấm và gấp thành hình như hình 5. Khi sử dụng, dùng kẹp để kẹp khuôn trên. Phương pháp này rất dễ sử dụng và có thể được sử dụng trong nhiều lớp.
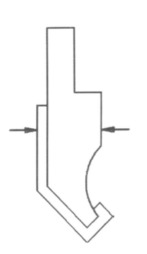
5) Một bộ phận và nhiều cài đặt khuôn
Zhongrui đã sử dụng máy uốn CNC DA66T với 2 xi lanh thủy lực làm minh chứng. Đã thử thiết lập nhiều khuôn thể hiện trong Hình 6, nghĩa là khuôn trên và khuôn dưới của cùng một mô hình được lắp thành từng phần cùng một lúc, điều này có thể hoàn thành việc xử lý một số đoạn uốn cong của toàn bộ bộ phận, giảm thời gian lắp đặt khuôn và xử lý lặp đi lặp lại các bộ phận. Hiện nay trên thị trường đã xuất hiện các loại khuôn trên có thể uốn cong chiều cao bằng nhau. Chiều cao của khuôn trên đều đồng nhất, và các khuôn có hình dạng khác nhau cũng có thể được sử dụng trên cùng một bàn. Bằng cách này, có thể thực hiện uốn phân đoạn các khuôn khác nhau.
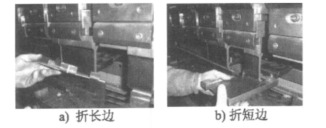
6) Hồ sơ chương trình của các phần tiêu biểu
Sau khi các bộ phận tiêu biểu được xử lý, các thông số xử lý cần được ghi lại kịp thời, và chương trình nên được lưu trữ trong khu vực lưu trữ của máy uốn với số bản vẽ bộ phận, để có thể sử dụng lại trong tương lai, giảm thiểu một loạt của các chế phẩm trước khi uốn. Bạn cũng có thể tạo một bảng, trong đó có các cài đặt cụ thể của tên bộ phận, số bản vẽ, đồ họa, vật liệu và các thông số uốn. Bàn được chia thành các loại tấm thép, tấm nhôm, và tấm inox. Mỗi loại được phân biệt bởi độ dày của vật liệu. Thời gian cần thiết để tìm các bộ phận tiêu biểu sẽ giảm xuống. Nếu kết hợp với thẻ quy trình, đây là một hướng dẫn xử lý rất đầy đủ. Ngay cả những nhân viên mới với ít kinh nghiệm cũng có thể làm theo lời nhắc để xử lý các bộ phận.
7) Chiều dài khuôn không đủ để uốn theo từng đoạn
Trong quá trình gia công tại chỗ, thường xảy ra hiện tượng chiều dài của khuôn nhỏ hơn mép uốn. Bởi vì nhiều khuôn đặc biệt được xác định theo việc sử dụng các sản phẩm cố định, phương pháp uốn phân đoạn được sử dụng khi chiều dài của khuôn nhỏ hơn cạnh uốn. Trường hợp chiều dài của khuôn gần với mép uốn, xé mép vuông góc với mép uốn, sau đó gấp mép uốn theo kích thước yêu cầu theo từng phần. Hình 7a là nửa bên trái của phần bị uốn cong và Hình 7b là nửa bên phải của phần bị uốn cong.

8) Sử dụng đinh tán trên máy đo lưng để định vị
Khi kích thước của chi tiết bị uốn lớn và sử dụng thước đo ngược để định vị, chi tiết thường bị chìm do trọng lượng bản thân, tay cầm của chi tiết ngắn và người vận hành không dễ dàng khi cầm phôi. Để đảm bảo mức độ của các bộ phận, một người điều khiển phải được bố trí ở phía sau quy tắc để giữ các bộ phận ở trạng thái bình độ bằng tay. Vì vậy, khi gia công các bộ phận đó phải bố trí 2 người vận hành. Trong công việc, người ta thấy rằng khổ sau có thể được hạ xuống một kích thước nhất định, và các đinh tán trên khổ sau được sử dụng để định vị, và các bộ phận được đặt nằm ngang trên khổ sau. Điều này không chỉ làm giảm số lượng người vận hành mà còn đảm bảo độ chính xác của quá trình gia công một cách hiệu quả.
9) Uốn cong hình dạng khép kín sâu
Trong thực tế gia công, gia công uốn hình dạng khép kín sâu có thể được sử dụng một cách linh hoạt. Trong trường hợp không có khuôn uốn sâu kiểu kín, khi uốn các bộ phận như trong Hình 7, trạng thái kẹp được chỉ ra trong Hình 8 được chấp nhận. Tách bảng chuyển tiếp, khoảng cách lớn hơn một chút so với chiều rộng của phần, và kích thước được phân bổ hợp lý, và có thể uốn cong hai phần cùng một lúc.
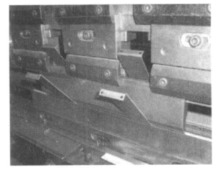
Các phương pháp và kỹ thuật chế biến được giới thiệu ở trên có thể giải quyết vấn đề gia công một số lượng lớn các bộ phận giống nhau trong sản phẩm và rất thích hợp cho việc phát triển các sản phẩm đa dạng, nhiều mẻ nhỏ và chu kỳ sản xuất ngắn. Thông qua các phương pháp này không những tiết kiệm được chi phí công cụ dụng cụ mà còn rút ngắn chu kỳ sản xuất, chế biến, hạ giá thành sản phẩm, nâng cao chất lượng sản phẩm. Các phương pháp gia công và kỹ năng sử dụng này cũng có thể được áp dụng và phát huy trên các máy uốn phanh dập CNC có kết cấu tương tự.